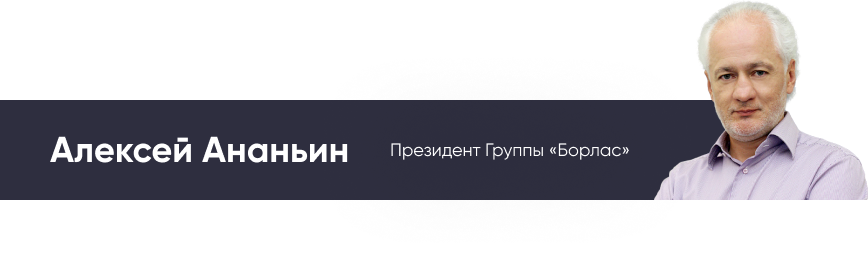
В 2019-м мы реализовали немало высокотехнологичных проектов, которые можно считать ступенями на пути создания полноценного цифрового производства для наших Заказчиков, представленных практически во всех этих индустриях. По итогам 2019 года наше PLM-направление показало заметный рост. У ряда Заказчиков мы выполняем целые серии проектов внедрения PLM-систем, охватывающих основные этапы жизненного цикла изделий.
Ключевая задача многих таких проектов — конструкторско-технологическая подготовка производства. В рамках одного из таких проектов прошлого года мы реализовали для компании — лидера в области проектирования и производства беспилотных летательных аппаратов очередной этап создания PLM-системы на базе Teamcenter от Siemens. Мы объединили две удаленные площадки — конструкторское бюро и производство — в единое цифровое пространство. Результат этой работы — повышение производительности труда и качества выпускаемых изделий за счет сокращения количества трудоемких для исправления комплексных ошибок, затрагивающих как конструкцию, так и документацию изделий.
По-прежнему актуальны задачи совершенствования управления предприятиями. Например, в прошлом году мы выполнили проект в Faberlic, решив приоритетные задачи по замене использовавшейся ранее информационной системы и построению единого контура управления предприятием на платформе 1С. В результате были автоматизированы операции учета и планирования производства, контроля качества сбора данных.
Среди наших заказчиков есть компании, с которыми мы сотрудничаем уже не одно десятилетие. Достигнув обозначенной цели в рамках одного проекта, мы, как правило, движемся дальше, способствуя повышению их операционной эффективности и конкурентоспособности. В прошлом году мы провели большую и очень интересную работу по модернизации внедренной ранее информационной системы на одном из крупнейших среди российских производителей стали предприятий черной металлургии. И сейчас участвуем в работах по объединению ряда его дочерних компаний в единое информационное пространство.
Для многих предприятий актуальны локальные задачи повышения эффективности отдельных производственных участков или технологических процессов. Например, задача стабилизации производственного процесса, сокращения количества брака и увеличения межсервисного пробега технологического оборудования. Подобный проект мы выполнили в «ЕВРОЦЕМЕНТ Групп», внедрив собственный программный продукт для автоматизации процессов технического обслуживания и ремонта оборудования (ТОиР). В настоящее время мы предлагаем рынку новую версию этого продукта — BRAMS (Borlas Repair & Maintenance System), обладающую расширенным функционалом. Основанная на алгоритмах предиктивной диагностики, она позволяет существенно повысить эффективность процессов ТОиР за счет перехода к более экономичному обслуживанию. По нашим оценкам и уже имеющейся информации от Заказчиков, использование BRAMS позволяет на 15% сократить количество внеплановых простоев и снизить на 10% затраты на приобретение и использование ремонтных ресурсов.
Если говорить о задачах текущего года, то сейчас мы ведем ряд крупных ERP-проектов. В качестве примера можно привести масштабный проект по разработке и внедрению корпоративной информационной системы управления ресурсами предприятий «Гознака», затрагивающий все ключевые бизнес-процессы.
В текущем году мы пока не наблюдаем каких-либо серьезных сокращений по программам цифровизации производств или существенных отклонений от планов наших Заказчиков. Делать какие-либо количественные прогнозы, не берусь, но в любом случае, можно сказать, что кризис, связанный с пандемией коронавируса, дал определенный импульс новому витку цифровизации и скорректировал тенденции рынка как в части технологий, так и компетенций его участников. И, как бывает всегда, кризис открывает новые возможности движения вперед, которыми мы и собираемся воспользоваться.