Портал «Управление качеством» проводит опрос экспертов российских производственных предприятий и IT-интеграторов о том, как применяются и как влияют аспекты Индустрии 4.0 на совершенствование и оптимизацию бизнес-процессов, управление производственной системой, уменьшение брака и снижение себестоимости продукции.
Тема сегодняшнего дня — контроль качества на современном предприятии с использованием технологии искусственного интеллекта и машинного обучения.
Мы побеседовали с Дмитрием Медовщиковым, архитектором IT-решений департамента цифровых и инженерных систем группы компаний «Борлас».
*Группа компаний «Борлас» — один из ведущих игроков IT-рынка России, уже более тридцати лет реализующий проекты цифровизации для своих заказчиков, представленных практически во всех индустриях.
УК — Дмитрий, насколько широко, по Вашему мнению, цифровые технологии сейчас используются в процессе контроля и управления качеством на современных производственных площадках?
ДМ — Сегодня Индустрия 4.0 предоставляет производителям новые инструменты для оценки качества выпускаемого продукта на всех этапах процесса. Цифровые технологии помогают отслеживать производственные процессы, собирать данные в режиме реального времени, применять аналитику для прогнозирования проблем с качеством и потребностей в обслуживании.
Контроль качества на современном предприятии охватывает всю производственную цепочку — от закупки сырья до выпуска готовой продукции и послепродажного обслуживания. Если говорить о пользе контроля качества изделия на всем производственном цикле, то он необходим как для раннего обнаружения брака, так и для выявления (и последующей ликвидации) причин отклонения от установленных стандартов. Вся информация, получаемая от системы контроля, представлена в цифровом виде и доступна в любой момент. Благодаря этому агрегированные данные с измерительных устройств сокращают время на проведение анализа полученных данных и затраты на их обработку без формирования регулярных отчетов вручную. Это существенно экономит время, повышает эффективность и скорость принятия решений, что, несомненно, способствует снижению себестоимости продукции.
УК — Если говорить о роли технологий машинного обучения и искусственного интеллекта в этом процессе, могли бы Вы привести в качестве примера такой кейс, реализованный Вашей компанией? С какими задачами обращаются заказчики, и насколько эти задачи различны?
ДМ — В трудоемком технологическом процессе применение машинного зрения в совокупности с алгоритмами глубокого обучения обеспечивает автоматизированный контроль оборудования, сырья и конечного продукта с выдачей последовательных и точных результатов. Машинное зрение минимизирует роль человеческого фактора, а также обеспечивает стабильный контроль в режиме «24/7».
Пример из практики — наш проект в одном из крупнейших предприятий нефтехимического комплекса России, где для заказчика в процессе производства брикетов каучука требовалось отследить и проконтролировать качество входящих в них гранул.
Гранулы (фото слева) производятся методом вулканизации и представляют собой синтетический эластомер. Их поверхность может содержать резиновые и металлические включения. Подобные дефекты могут стать причиной отбраковки готового изделия, что в итоге приведет к дополнительным потерям, связанным с повторной переработкой сырья. Суть технологии машинного зрения в том, чтобы в процессе движения гранул по виброконвейеру в пресс зафиксировать посторонние включения размером 3×3 мм и исключить попадание дефектных гранул в резервуар пресса.
Однако контроль гранул — это только часть функций системы. В процессе формирования (после температурной обработки) поверхность брикета каучука приобретает уникальную фактуру и изобилует всевозможными трещинами, потемнениями и т. п. Обнаружение этих дефектов осуществляется непосредственно на производственной линии. До внедрения системы машинного зрения контролем качества занимался человек, который постоянно находился у конвейера и визуально фиксировал наличие дефектов, занося вручную данные в соответствующий журнал. В некоторых случаях часть продукции с включениями отбраковывалась с запозданием, уже на складе, и возвращалась на переработку с большой задержкой.
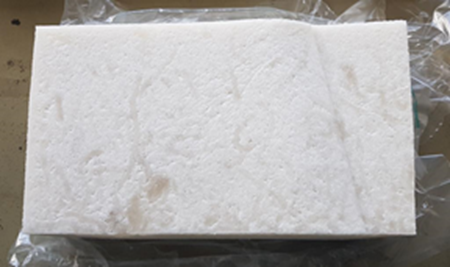
Наше интеллектуальное решение позволило проконтролировать качество на всех этапах формирования готового изделия. Отбраковка производится путем проверки гранул перед началом формирования брикетов, а также за счет сканирования поверхности готовых брикетов на конвейерной линии. Автоматизированное ведение журналов ОТК и учет готовой и отбракованной продукции позволили сократить издержки производства, связанные с повторной переработкой. Это высвободило время персонала, затрачиваемое на заполнение журналов и позволило существенно оптимизировать затраты.
В качестве другого примера внедрения технологии машинного зрения можно привести наш проект для одного из ведущих в России предприятий черной металлургии.
Здесь требовалось разработать систему неразрушающего контроля сталеплавильного производства. Необходимо было сократить простои дуговой сталеплавильной печи в процессе выплавки металла.
Плавка стали производится в рабочем пространстве печи, которое ограничено сводом и подом, а его стенки выложены изнутри огнеупорным материалом. Через три симметрично расположенных в своде отверстия в рабочее пространство печи введены токопроводящие графитовые электроды, которые перемещаются вверх и вниз при помощи держателей. Температура в печи во время плавки достигает 1800 градусов Цельсия. В процессе выплавки электроды могут получить повреждения вследствие воздействия шихты или подачи напряжения, которое не соответствует их сечению. В результате на поверхности электродов появляются трещины, что влечет за собой разрушение их рабочей части и производственные потери, связанные с остановкой печи и необходимостью замены электродов.
Наша команда разработала MVP-систему мониторинга электродов дуговой сталеплавильной печи, которая построена на базе алгоритмов искусственного интеллекта с применением промышленных камер, в том числе коротковолновых. Система предназначена для обнаружения дефектов на рабочей поверхности электродов, образовавшихся в процессе выплавки стали. Решение реализовано на базе ПО и оборудования российского производства. Рабочая поверхность электрода при нагревании приобретает уникальную фактуру и начинает светиться. Это не позволяет человеческому глазу распознавать имеющиеся на рабочей поверхности электрода дефекты. Но для электроники такой проблемы не существует.
УК — А как работает эта система?
ДМ — В процессе выплавки стали система контролирует характер и силу горения электрической дуги, сопоставляет мощность, подаваемую на электроды, с их диаметром и дает сталеварам рекомендации по уменьшению нагрузки в процессе плавки для предотвращения разрушения электродов в печи.
Дополнительно комплекс анализирует рабочую зону электрода на наличие повреждений, которые могут образоваться при выплавке «колодца» (рисунок 1 — отсутствие повреждений; рисунок 2 — наличие повреждений в рабочей зоне). Комплекс фиксирует и анализирует повреждения, после чего выдает необходимые рекомендации.
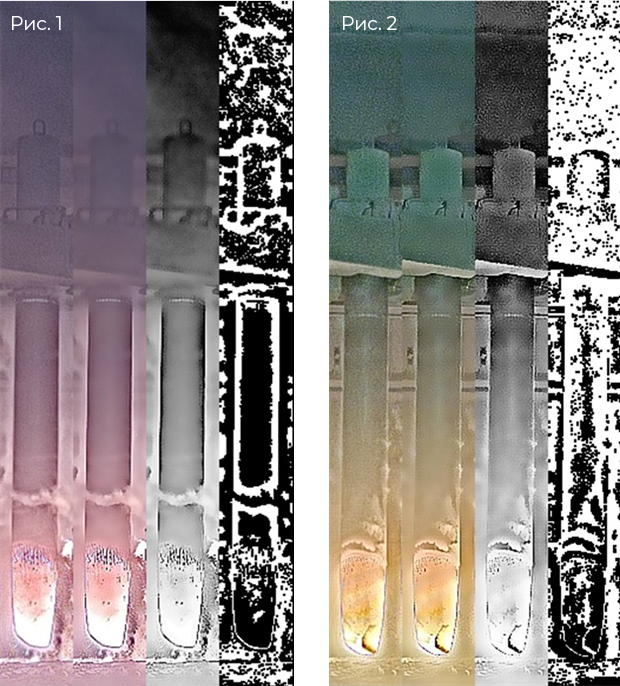
УК — Правильно ли я понимаю, что каждый такой проект — это своеобразный «конструктор», состоящий из разных решений и подходов?
ДМ — Суть реализуемых нами проектов состоит в том, чтобы создать индивидуальное цифровое решение под конкретные задачи заказчика. Для этого мы проводим аудиты, тщательно изучаем инфраструктуру, специфику бизнес-процессов заказчика и всегда работаем с ним «в тандеме». По завершении проекта проводим обучение пользователей и можем организовать необходимую техническую поддержку новой системы.
УК — А насколько сложно в сегодняшних санкционных условиях реализовывать подобные проекты?
ДМ — Во-первых, у нас достаточно объемный портфель решений от отечественных вендоров, которые не уступают зарубежным.
Во-вторых, мы всегда занимаемся поиском и выстраиванием взаимоотношений с альтернативными поставщиками технологий и компонентов.
В-третьих, мы непрерывно пополняем продуктовый портфель собственными уникальными разработками, поэтому на сегодняшний день непреодолимых сложностей я не вижу.
Спасибо за беседу!